GEA is the technological leader for dynamic high pressure homogenizers and plungers pump in several different industries and applications. Homogenization is a key well known process in dairy, food & beverage industries, nevertheless new markets are growing thanks to continuous innovation and research.
New products such as cellulose and carbon nanotubes arouse more and more interest as well in this scenario. Higher stability on products is one of the most important effects achievable through this process.
The stable emulsion which is delivered as outcome, is a viscous final product characterized by enhanced organoleptic properties, taste, glossy colour and shelf-life.
The passage through the homogenizing valve enable to avoid separation phenomena on particles, increase the digestibleness of processed products and the assimilation of the nutritional principles, especially for infancy and functional food industry.
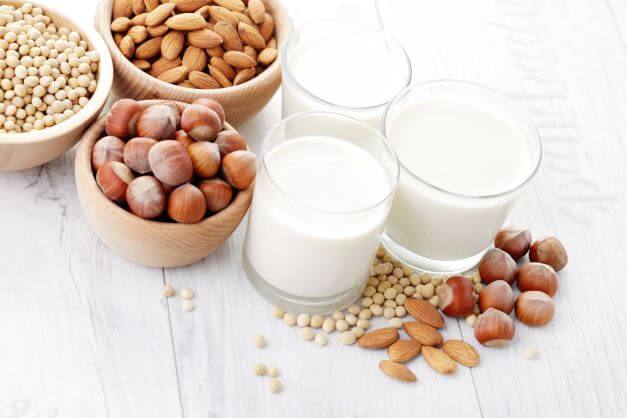
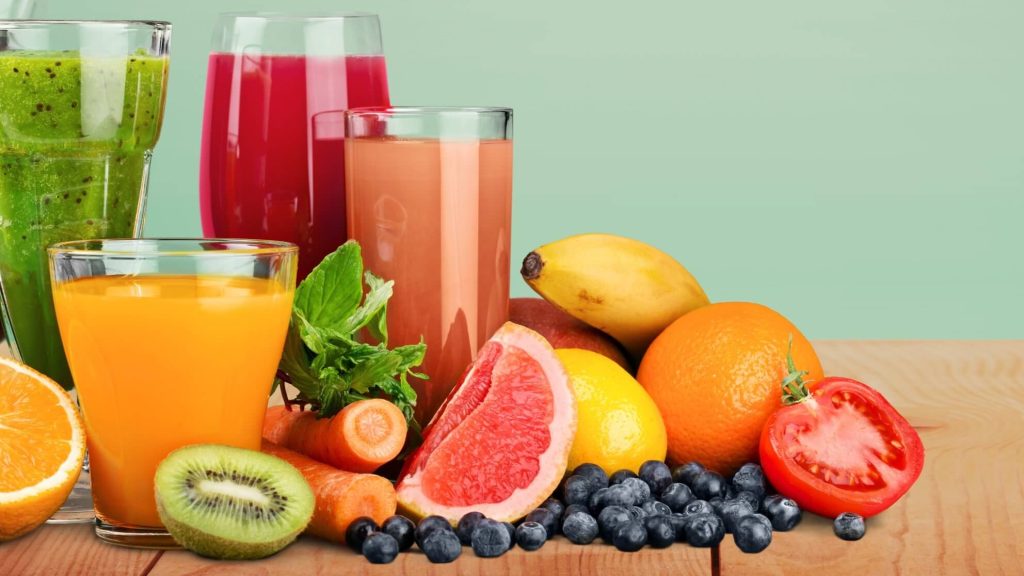
Wide range of homogenizers
GEA can offer a complete range of high pressure homogenizers, from laboratory up to industrial scale, providing more than 300 options to satisfy market’s and customer’s needs. All the machines meet the most stringent hygienic requirements and quality control systems. All homogenizers are CIP and SIP’able and are available with cGMP documentation.
The new GEA XStream Lab Homogenizer: the XStended version of innovation
GEA XStream Lab Homogenizer is table top unit designed to carry out tests in laboratory and be prepared to scale up to the industrial production the consistent results that NiSoX-Valve provides for many and different applications. The ergonomic design of this machine conceived for a perfect fit on standard lab desks ensures smart and easy operating conditions.
The most innovative advantages of this homogenizer are the intuitive PLC configuration and the self-adjusting pressure feature which provide optimized high quality efficiency with 100% trials repeatability thanks to automation.1 The GEA XStream Lab Homogenizer it’s a safe, smart and simple homogenizer with high level of automation.
The new GEA Homogenizer Compression Block NiSoCLEAN 2.0
If hygienic design and excellent high pressure performances are what you’re looking for, Ariete Series homogenizers configured with the improved compression block NisoCLEAN 2.0 are the right solutions to meet your requirements.
This optimized configuration has been conceived in order to satisfy the increasing food & beverage market’s demand and improve cleanability procedures, optimizing easy maintenance of the machine and always ensuring reliability.
Industrial homogenizers
Ariete Series homogenizers are the state-of-the-art technology for powerful, reliability and customized solutions and they are suitable for several industries. These are ideal to process dairy, food, beverage, pharma, biotech and chemical products.
The homogenizing pressure can reach 1500 bar depending on specific liquid end design and configuration. The homogenizers from the One Series combine convenience and absolute quality to deliver unmatched benefits.
These 3-piston homogenizers are manufactured to ensure easy maintenance and simple installation into small-medium productions of dairy products, beverages and soft chemicals.
Laboratory homogenizers
Pilot plant homogenizers are designed for continuous operation up to 1500 bar and limited productions easy plug & play installation, simple operation and quick maintenance. Table-top homogenizers are compact machines ideal for the treatment of nanoparticles, nan dispersions and nan emulsions up to 1000 bar.
Customer collaboration
The close collaboration with important customers R&D centers, and continuous improvements on production technologies, allow the company to invest in close collaboration with customers which lead to the continuous implementation of innovative and tailor-made solutions.
The recently refurbished Process Technology Center is a unique resource to test homogenization technology, refine receipts, develop high efficiency homogenizing valves and evaluate the performance of installed machines.
We are glad to be able to offer to customers more comfortable meeting rooms and cutting edge instruments. Highly qualified staff can support customers in the development of new products, to test maximum process efficiency conditions and product scalability to industrial production processes.