The global population relies on the agricultural sector for food security, making efficient and sustainable production vital for human life. Organic farming with integrated pest management is a focus area for the industry, but the reliance on internal combustion engines (ICEs) harms the health of farm workers and contaminates products. At the same time, fuel forms a substantial portion of the sector’s operating costs.
These machines emit pollutants, such as CO2 and particulates, which are harmful to operators and can contaminate plants, leaves, flowers, and fruit. Furthermore, fuel systems can rupture, causing a spill, thus contaminating the soil and future production. Diesel machines also emit high noise levels, which harms humans in the vicinity.
Pitteri Violini is a leading supplier of components, engines, and end-user machines for the construction and agricultural sectors. Known for its quality, originality, and excellent design features, Pitteri Violini has been making self-propelled machines for more than ten years. Its pioneering fruit-picking tractor already offers self-levelling features for fruit picking in mountains and hills. Electrifying this machine builds on its tradition of customer service and innovation to create sustainable machines for the agricultural sector.
Parker Hannifin, a global motion and control technology company, supplied several components for the electric fruit-picking tractor, along with extensive design and consulting services. The highly efficient GVM motor and GVI inverter allowed Parker to design a solution that meets the requirements of operating for a complete shift without the need for recharging.
The initial phase of this project was a direct replacement of the diesel power generation with an electric equivalent. However, future models of this machine will optimise the machine and offer even greater benefits.
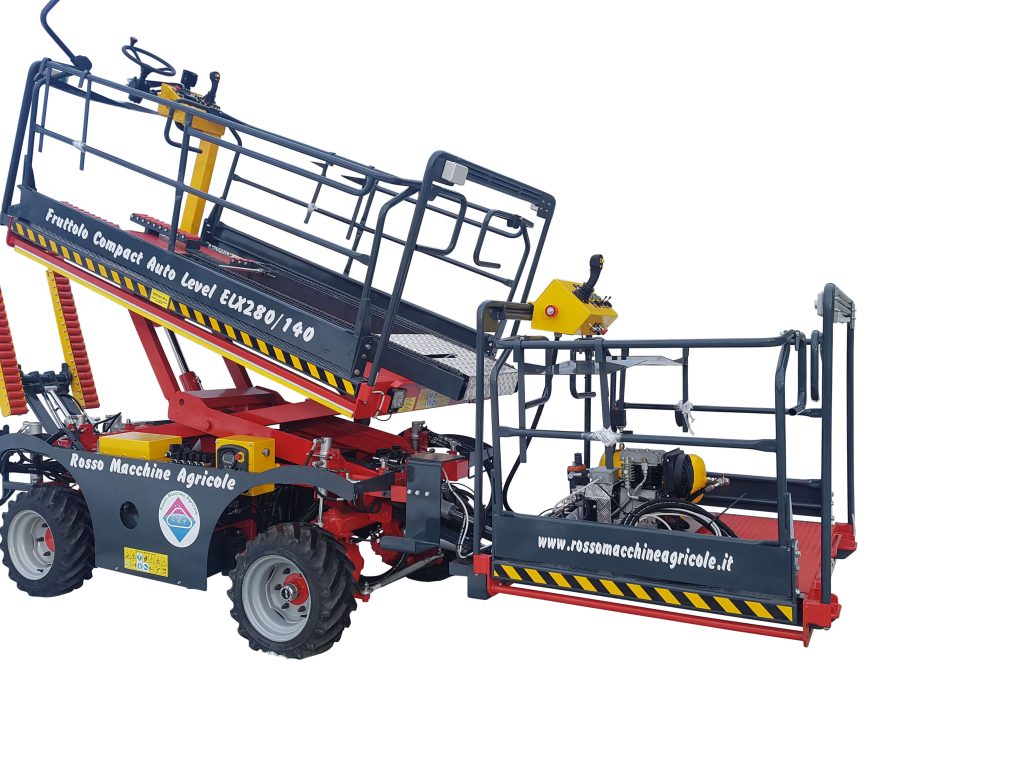
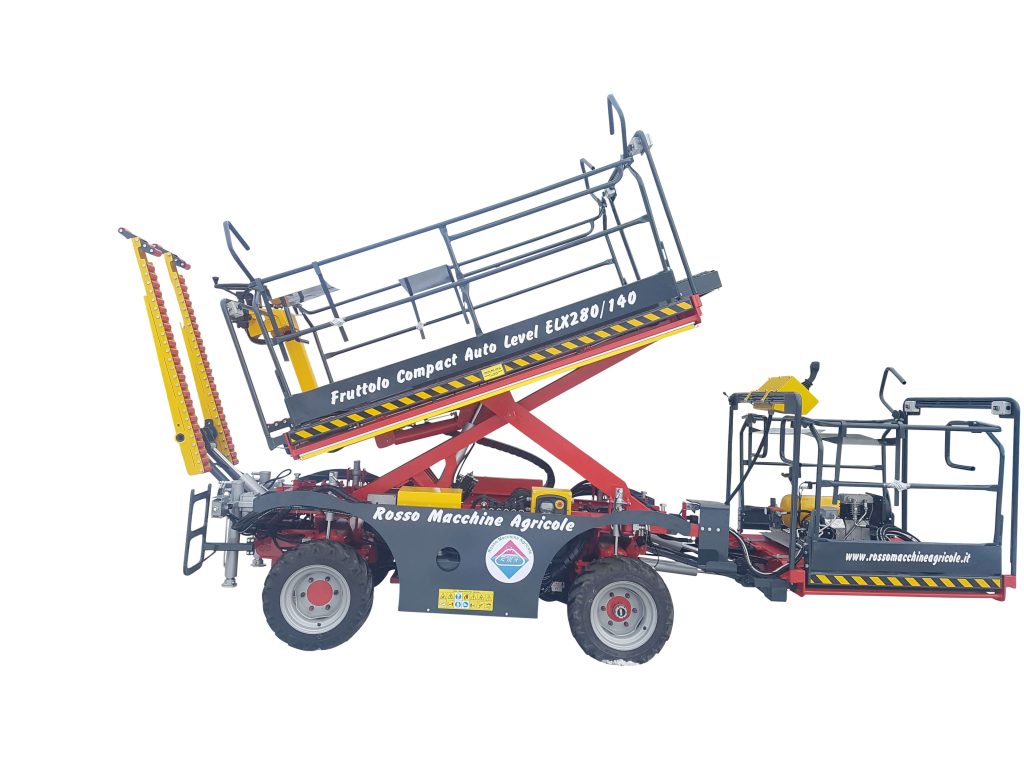
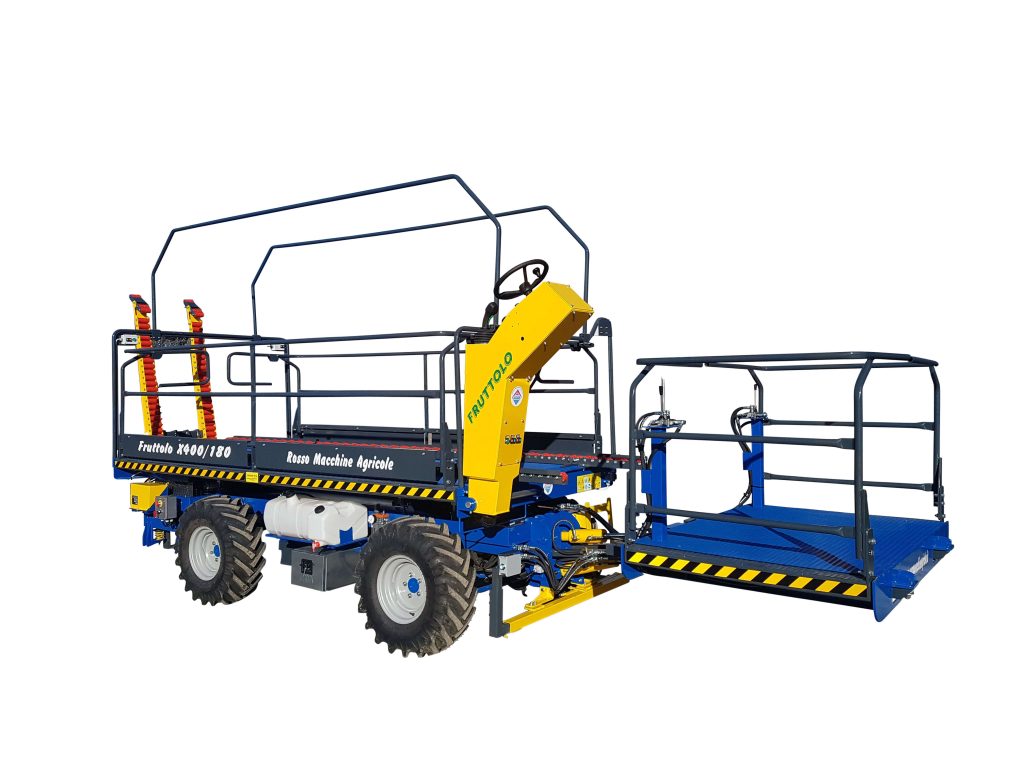
The challenges to making electric agricultural machines
As with the migration of any heavy machinery, the limit of battery capacity often hinders the migration from diesel-powered engines to electric motors. Agricultural machines operate at long distances from the main farm infrastructure making it impractical to recharge the machines during a working shift. Any loss of time for recharging also significantly reduces the productivity of the operation.
In addition, the agricultural sector employs many unskilled workers who are familiar with simple, mechanical machine functions without complex human interfaces. Electric machines must mimic this simplicity in order to make the transition to electric machines as smooth as possible. Training and development of operators in the agricultural sector is an essential element in the transition from hydrocarbon fuels to electric machines.
The fruit-picking tractor was the ideal candidate for electrification due to its small size and lower power demand than other machines. Nevertheless, its compactness made it challenging to fit the electric components and battery onto the chassis without modifying the design. This machine operates in direct contact with the fruit and in close proximity to several operators at any time, so the electrification of the tractor will make an immediate health and product quality impact.
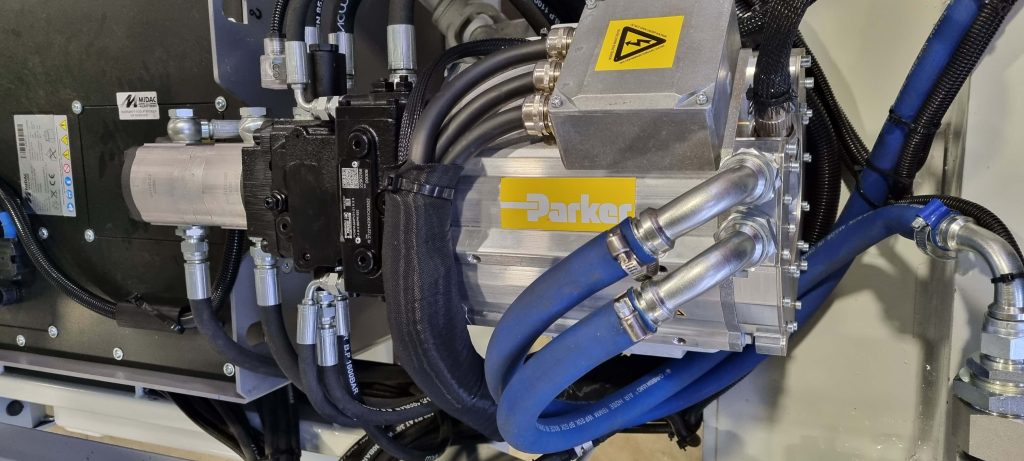
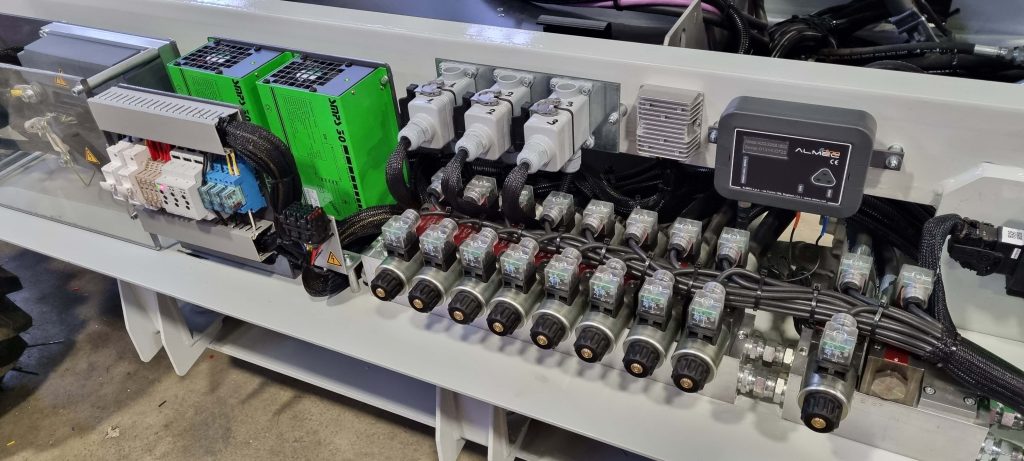
The electric technology behind the fruit-picking tractor
The electric solution for the fruit-picking tractor is designed as a low-voltage system using a 96 V battery. This approach allows for a simple solution that is easy to manage. Parker supplied several components for the fruit-picker, with the main items listed below:
- GVM210.100.DPW motor: This motor replaces the diesel engine and provides power for driving the machine as well as auxiliary hydraulic functions. Its high power density and high efficiency make it a well-suited solution for this application.
- GVI.E096.700 inverter: This low-voltage motor controller offers a combination of power, performance, and functionality. Its compact dimensions and high efficiency make it ideal for integration into limited spaces, and the high-efficiency cold plate design means the inverter does not require external cooling.
- QDC007 cooling system: A thermal management system consisting of an air fluid heat exchanger, water pump, pipes, and sensors provides cooling for the GVM motor. The system automatically controls the temperature of the liquid cooling system.
- IQAN-MD4 controller and display system: The IQAN management system controls the machine function and allows operators to modify parameters using the 7-inch human interface display. Operators can also use the joystick provided to operate the machine precisely as they would the previous diesel-driven version.
Parker selected the specific electric components with the functionality and mechanical configuration of the fruit-picking tractor in mind. It was a requirement of Pitteri Violini to maintain the mechanical configuration of the original ICE tractor, and the GVM motor and GVI inverter were critical to achieving this objective. The prototype version of this machine meets the primary objective of replacing the hydrocarbon energy source with electricity but also lays the platform for optimization in future models.
A collaborative approach
Pitteri Violini has a long history of innovation in terms of agricultural machine design and construction. The team’s dedication to optimising machines according to customer requirements led to the cutting-edge design of the self-propelled and self-levelling fruit-picking machine for mountainous and hilly terrains. The company applied the same dedication and innovation working with Parker to electrify this machine.
On the other hand, Parker Hannifin has been developing technology and components for mobile machines for more than 100 years. The company’s expertise covers the technical details of electrification components as well as the vast experience of how mobile machines work in a wide range of applications.
Parker and Pitteri Violini collaborated on the fruit-picker’s electrification by analysing the performance of the ICE machine and the datasheet of the diesel engine. Hydraulic flow and pressure data were converted to energy, which formed the basis for selecting the GVM motor and GVI inverter – a very high-efficiency solution. The minimum battery capacity was specified based on the power consumption data from the GVM and GVI and the requirement to meet the tractor duty cycle requirements.
This initial collaboration between Parker Hannifin and Pitteri Violini aimed to electrify the fruit-picking tractor without any enhancements. However, future collaborations will completely redesign the hydraulics system in a two-motor optimised solution. One motor will provide the power for traction, while the other will supply the auxiliary functions. This approach will save a substantial amount of energy and enable the use of the Parker NX8 range of motors designed for mobile applications with low voltage. In preparation for this next phase of electrifying the fruit-picker, the current system is collecting data on power consumption, flow, temperature, and other parameters on a time basis and correlating the data to the machine function at that time.
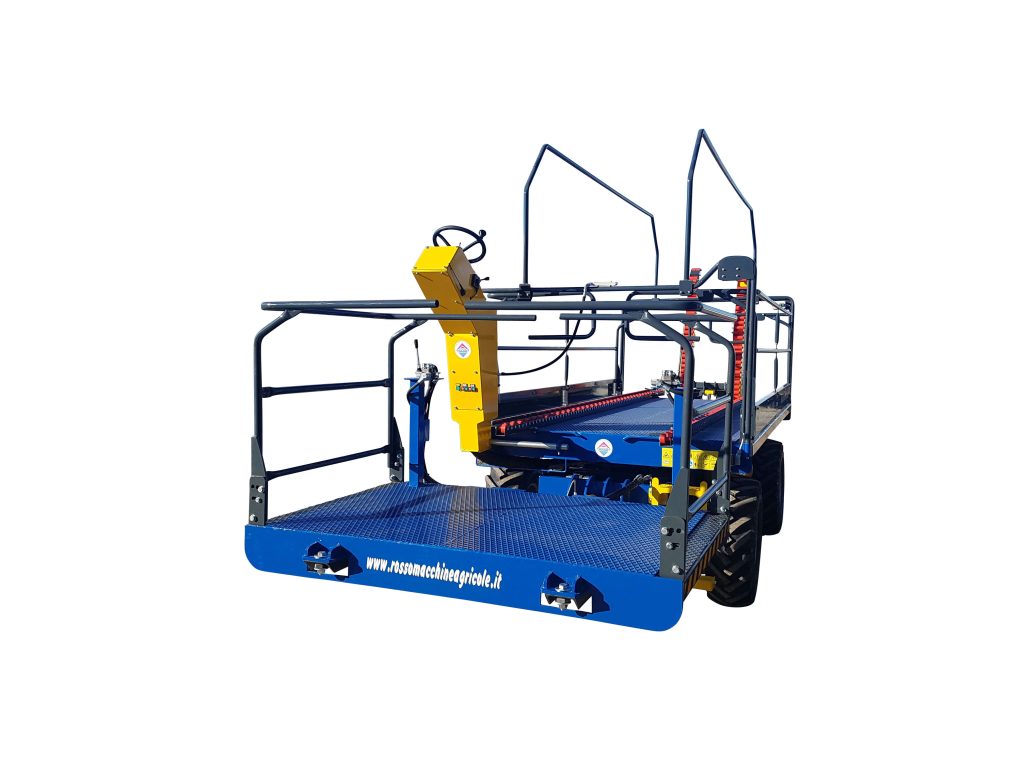
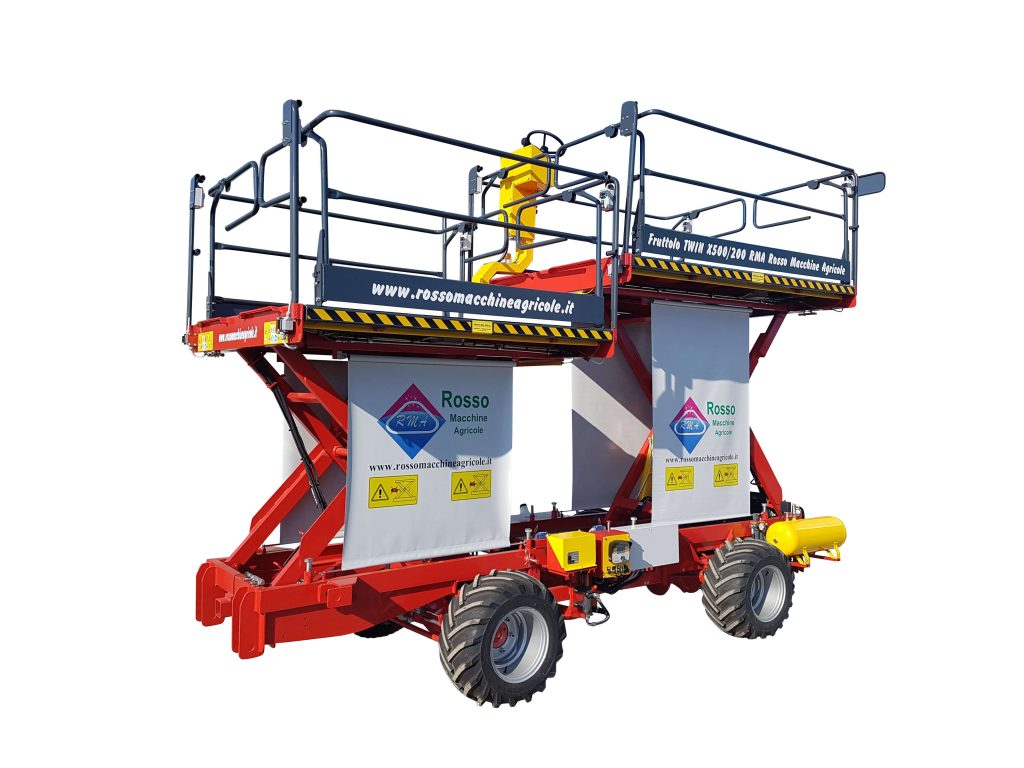
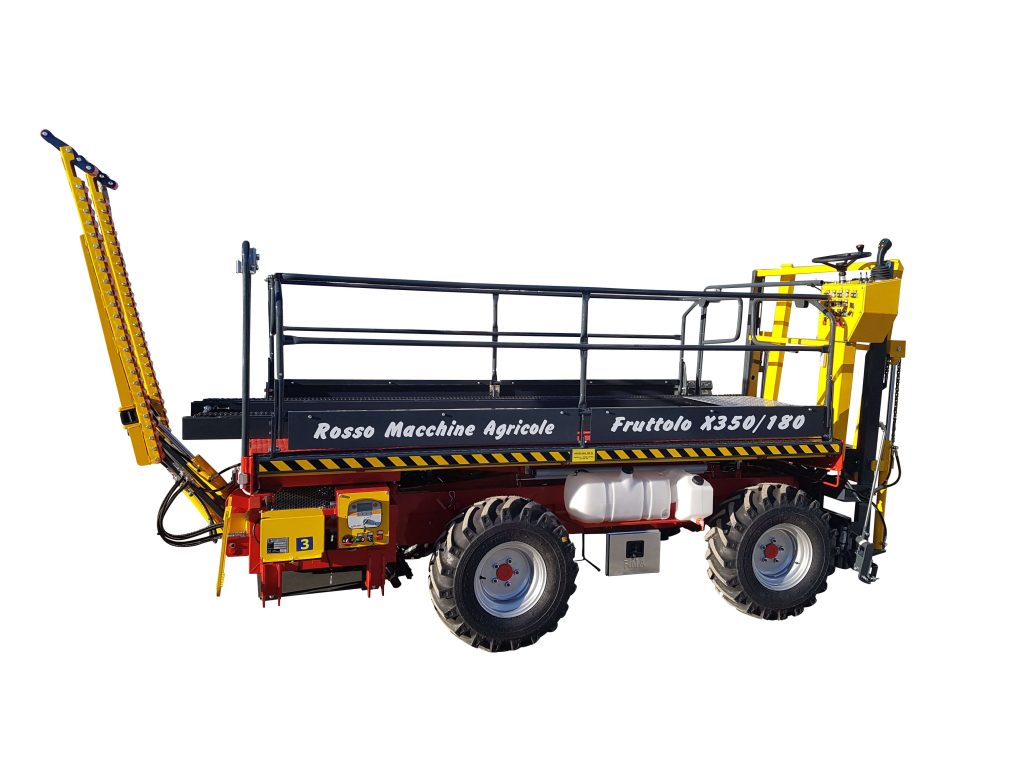
The benefits of electric agricultural machines
The electrified fruit-picking tractor is delivering outstanding results in terms of exhaust emissions and noise. The noise levels around the machine have dropped from 80 dB to just over zero. This change has made an immediate change to the comfort and risk of long-term hearing loss to operators. Exhaust emissions have been reduced to zero as there are no fossil fuels used on the machine. This means that operators are no longer exposed to harmful CO2 gases and particulates, and fruit is free of contamination.
Moving away from diesel-powered engines has also lowered the operating costs by 80% for the machine user. This massive improvement has been achieved without compromising on machine availability. The electric fruit-picking tractor runs for 12 to 14 hours after charging for eight hours at 220 to 380 volts.
The IQAN management system has also delivered significant benefits for machine users. IQAN allows operators to operate the machine, modify parameters, and access information. The system collects data from sensors about hydraulic pressure, flow, and temperature. It also accesses data from the inverter about voltage, current, and battery performance. In the future, this data can be used to analyse the machine’s performance as well as generate predictive maintenance advice. Adding IoT devices will enable remote assistance via the cloud.
Based on the success of this project, Pitteri Violini plans to electrify ten fruit-picking tractors each year in order to transition the diesel-powered fleet to a more sustainable technology. The program will also be extended to other machines so that the entire industry can be decarbonised over time.
Conclusion
Pitteri Violini and Parker have combined their expertise in agricultural machines and motion and control technology to develop an electric fruit-picking tractor. This project is the first step in a journey of transitioning the sector from legacy fossil fuel energy sources to a sustainable future.
The electric fruit-picker has made an immediate environmental impact by reducing exhaust emissions to zero and noise levels from 80 dB to just over 0 dB. At the same time, operating costs have reduced by 80%.
Pitteri Violini said : “While there remains an economic gap between an electric application and one driven by an endothermic engine, the road to decarbonisation has been mapped out, and there will be an increasing demand for zero-emission machinery. Pitteri Violini, will be at the side of small-to-medium domestic manufacturers, supporting them in the transition to increasingly sustainable applications thanks to Parker and its broad product portfolio.”
About Parker Hannifin
Parker Hannifin is a Fortune 250 global leader in motion and control technologies. For more than a century, the company has been enabling engineering breakthroughs that lead to a better tomorrow. Learn more at www.parker.com or @parkerhannifin.
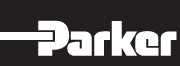