Packaging has been playing a key role in the marketing strategies of all companies of the industry and has increasingly been the focus of attention of a series of European directives that promote the use of renewable materials.
The pack plays an equally important role, as it ensures product protection and safety, avoiding damages and contamination during transport and storage.
For this reason, food & beverage companies pay great attention to the packaging solutions to be used in their plants and increasingly invest in environmentally sustainable and energy-efficient production technologies, like those presented by SMI during Drinktec trade fair last September 2022.
New EBS KL stretch-blow moulder: compact, fast and efficient
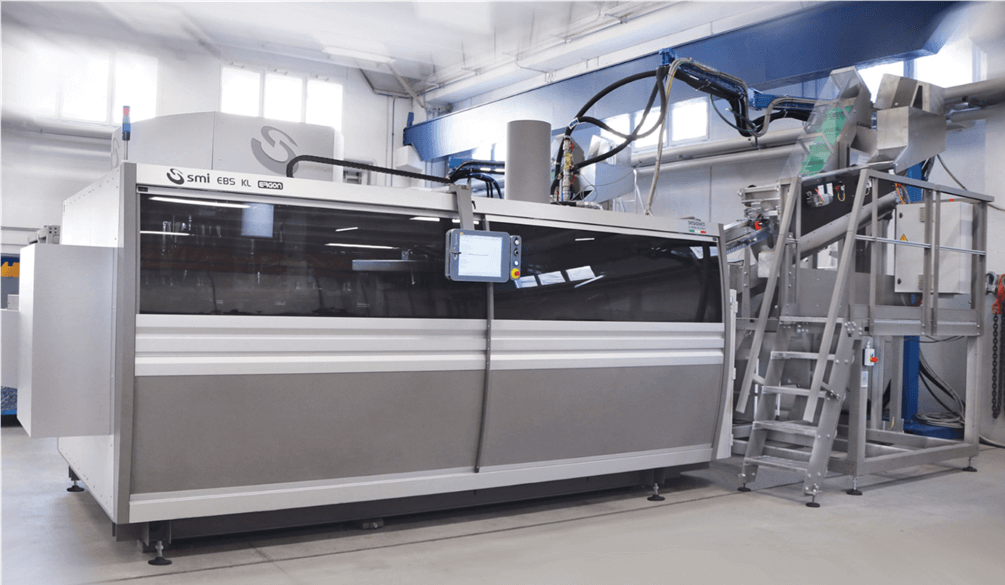
The latest example of such innovations is represented by the new compact EBS KL ERGON rotary stretch-blow moulder. The project has begun after the success of several technical innovations introduced on the stretchblow moulders from the EBS K ERGON range that has met for several years the needs of a growing number of middle-sized companies within the primary packaging sector.
The need to meet the requirements of higher production speeds led SMI designers to develop the new series of ultra-compact rotary machines called EBS KL ERGON (where the letters KL stand for “Kompakt Large”), suitable for meeting production requirements up to 25,000 bottles/hour.
The new series is composed of models up to 10 cavities for the stretch-blow moulding of PET / rPET / PP / PLA containers up to 3 liters, available in stand-alone as well as in ECOBLOC® version, integrated with electronic filler and capper and three models for the stretch-blow moulding of high-capacity containers up to 10 litres.
EBS KL: compact and high-performance stretch-blow moulders
The new compact blow moulder by SMI is a cutting-edge technical solution that stands out in the reference market for a wide range of advantages: the preform heating section (heating tunnel) is integrated with the stretch-blow moulding section (carousel) into a single, very compact module that makes the system suitable for the installation even in small bottling lines.
The main features of the new range are:
• production speed up to 2,500 bottles/hour per mould (0.5 L format);
• the structure that embeds the heating tunnel and the carousel is equipped with slightly rounded safety doors, which increase the space inside the machine in order to perform cleaning and maintenance operations easily and safely;
• the stretch-blow moulding carousel is equipped with motorized stretch rods, whose functioning, controlled by electronic drives, does not require pneumatic cams; this ensures a precise management of the stretch rod path and an accurate control of its position, as a well as a considerable energy saving;
• thanks to the cam-free technology it is possible to modify the stretch speed without mechanical interventions as the servo-motor automatically adjusts according to the production speed (up to 2.4 m/s). This solution reduces the machine vibrations and the adjustments to be performed in case of format changeover;
• thanks to its compact structure, EBS KL blow moulder can be easily transported in a container, thus saving on transport costs;
• the compactness also simplifies the installation and set-up operations, that are performed in about two days of work, ensuring a great quality-price ratio;
• the stretch-blow moulding system uses high-performance valves with low dead volumes (-50%), that reduce the pre-blowing and blowing times, with advantages in terms of machine performance and quality of the bottles produced;
• the mechanical unit of the mould is equipped with its own motorization, that performs with the utmost precision the up/down-motion of the mould bottom and the opening and closing operations of the mould holder unit;
• use of plastic bearings that reduce the wear and the vibrations to which the grippers are subject and do not require lubrication;
• the adjustment of the blowing pressure according to the bottle format is automatic with undoubted advantages;
• air recovery single-stage system installed as a standard device;
• plant managed by Motornet System® automation and control system that ensures the constant maintenance of optimal working parameters during the whole production cycle and the direct modification of the machine parameters and easy format changeover operations;
• simple and intuitive Posyc® operator interface, that uses advanced software for the management and diagnostic of the production efficiency, energy saving and predictive maintenance
• the machine is equipped with an energy consumption counter that allows to detect the electric consumption of the heating tunnel
Innovative preform heating tunnel
EBS KL ERGON stretch-blow moulding system is equipped with an innovative preform heating tunnel with an extremely compact design that is integrated with the stretch-blow moulding carousel into the same machine module and stands out for several advantages:
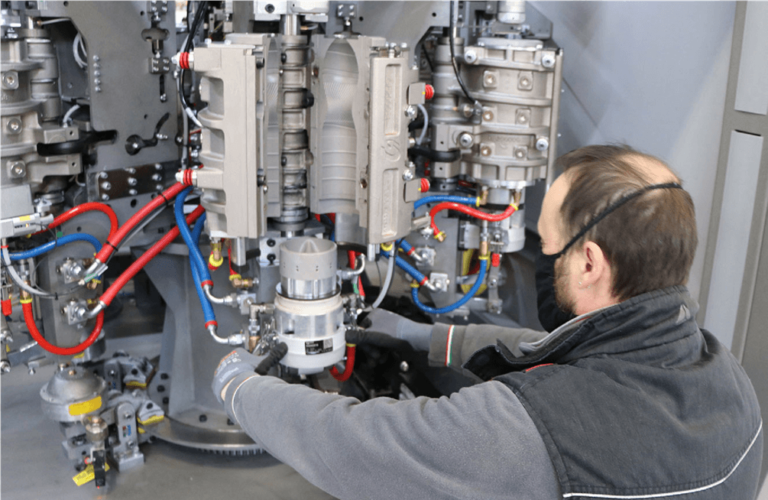
• the compact design ensures high speeds despite the reduced space;
• the preform feeding system is equipped with adjustments by means of position numeric counters, that speed up the format changeover operations;
• staggered position of the spindles which allows to adopt optimized chain pitches according to the preform diameter and to shorten the heating tunnel length, thus reducing the number of preforms inside the heating tunnel, as well as the waste and the consumption;
• the preform gripping spindle unit is equipped with a new system of diffusers, without spheres and with gasket, for the heat dissipation, which allows to significantly reduce the component wear;
• the infrared lamp units for heating the preforms in transit are equipped with thermo-reflective panels made of highly energy efficient ceramic material, placed on the lamp front and rear. This solution ensures a high reflection of the heat generated by a more uniform distribution of the heat over the entire surface of the preform;
• new ventilation system of the heating tunnel equipped with high-capacity centrifugal fans, that take fresh air from the bottom and channel it to preform body and neck. This system reduces the temperature of the preform neck with advantages in terms of thickness optimization and elimination of the ovalization and deformation of the preform neck and ring.
Plastic-free solution for the secondary packaging
Starting from some features of the packers in overlapping cardboard sleeves from the MP ERGON range, SMI has developed a new multipack packaging machine called TPP ERGON (acronym for Top Pad Packer).
Designed for those bottlers who want to use plastic-free solutions, the TPP 300 ERGON model, is the ideal solution for getting efficient and high-speed productions, up to 300 packs/minute.
The new TPP automatic packer is a smart packaging solution that stands out for the respect for the environment, the advanced automation and the flexible use. It has been developed for the secondary packaging of several types of cans by means of the application of a cardboard pad placed in the upper part of the pack.
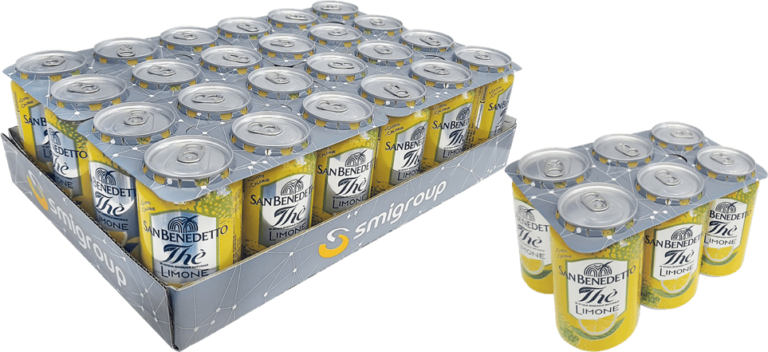
In the pack formation area, the cans are grouped in a continuous way in the desired format through electronically synchronized separation devices. At the same time, a flat cardboard pad is placed over the cans in transit by means of an interlocking system.
The flat cardboard pad is picked by the cardboard magazine and positioned in the upper part of the system, by means of a rotary picker. The multipack created by the TPP ERGON is an alternative to the traditional packaging solutions in overlapping cardboard sleeves produced by the machine from the MP ERGON range and to the packs made by the packers in shrink film.
The new multipacks, that do not require the use of glue, meet the growing market demands for environmentally sustainable solutions and the needs of the companies of efficient, flexible and competitive packers.